精益生产是一种生产管理方法,起源于日本丰田汽车公司,核心是追求消灭包括库存在内的一切“浪费”,并围绕此目标发展了一系列具体方法,逐渐形成了一套独具特色的生产经营管理体系。在美国麻省理工学院的一项名为“国际汽车计划”的研究项目中提出后,精益生产成为现代制造企业的一种生产组织管理方式,综合了大量生产与单件生产方式的优点,在大量生产中实现多品种和高质量产品的低成本生产。
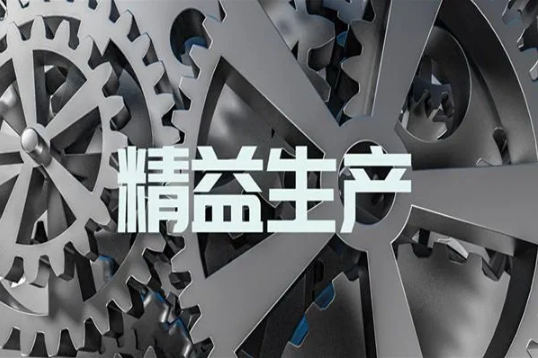
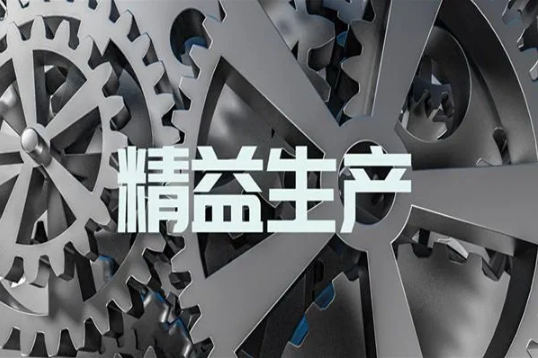
精益生产的核心思想:以全过程的高质量为基础,通过消除产生质量问题的生产环节来“消除一切次品所带来的浪费”,追求零不良,并且在现有基础上进行持续地改进。
精益生产的基本原理:通过查找和消除生产过程中各种各样的浪费现象,达到降低生产成本的目的。
精益生产的特征:
1、准时的生产方式:精益生产采用拉动式生产方式,根据客户需求实时生产,杜绝过量制造,减少浪费,降低成本。
2、适度自动化的生产方式:精益生产中的自动化是指赋予机器以人的智慧,出现异常就立即停机,防止生产次品,防止不合格的产品从前道工序流入后工序,及时制止过量制造,能自动控制现场发生的异常情况,自动监视和管理不正常的情况,使人从机器旁解放出来,是保证准时生产的手段。
3、“拉式”生产方式:精益生产采用“拉式”生产方式,后工序人员去前道工序领取需要的零件,前工序工人只生产后工序所需数量的零件。
4、看板方式:精益生产采用看板方式进行生产,需要零部件的人,去拿所需的零部件时,在看板上将状况记录上去。生产零部件的工人,则按上面记录的数量来生产。
5、多技能工化:在精益生产中工人都要成为至少能负责2种以上工作的多技能工。多技能工可以使生产计划更富有灵活性。
6、坚持持续改善:持续改善是精益生产的核心。虽然完全消除浪费是不可能的,但是精益生产方式敢于向完美挑战。精益的目标就是库存为零,浪费为零,利润最大化。
精益生产的作用:
1、提高交付能力:精益生产基于顾客需求的拉动式生产,追求在需要的时候按所需要的数量生产,通过强化供应链,按照生产节拍,依销售的需求速度来进行生产,同时保持物流的平衡,任何过早或过晚的生产都会造成浪费。
2、标准化管理:标准化是精益生产的基础之一,它将企业中最优秀的做法固定下来,使得不同的人来做都可以少出差错或不出差错,做到最好,发挥最大成效和效率。
3、保障安全:通过5S管理打造规范、可视化的现场,员工能遵守标准作业并依据要求工作,安全当然能得到保障。
4、提高质量:精益生产认为,质量是企业价值与尊严的起点。质量是制造出来的,而不是检验出来的。
5、优化流程,提高总体效益:好的流程就能够产生出好的结果。
6、提升效率:精益通过持续的改善,消除所有环节的浪费,包括不增值的活动和异常损失。
免责声明:本网站部分文章、图片等信息来源于网络,版权归原作者平台所有,仅用于学术分享,如不慎侵犯了你的权益,请联系我们,我们将做删除处理!
推荐资讯
产品系列